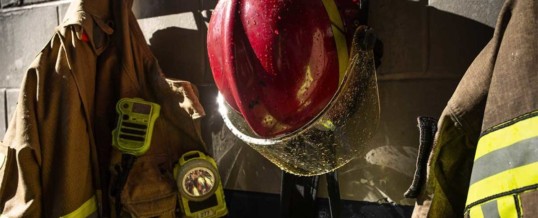
Grain dust explosions and stored grain fires remain frequent causes of severe damage to and loss of facility structures, equipment and inventory. Tragically, employees are often injured and killed.
Purdue University catalogues the annual number of deaths and injuries from grain dust explosions in the United States. In 2020, eight incidents occurred, nine people were injured but fortunately there were no fatalities. The 10-year average for explosions is 8.1 with 8.1 injuries and 1.7 fatalities. During the past decade, dust explosions occurred most frequently at grain elevators (46 out of 81) with corn the most frequently handled grain type (39 out of 81). The state of Iowa is where most grain dust explosions have occurred during the past 10 years (9) and since 1958 (98) followed by Illinois (86) and Nebraska (82), all major corn producing, handling, storage, processing and utilization states.
A recent series of white papers by US-based Nationwide Mutual Insurance Co., with input from its Nationwide Grain Advisory Board, addressed pre- and post-fire grain issues and an initial response plan when fires erupt in stored grain. Best stored grain monitoring and management practices are the most effective ways to prevent grain fires. We have covered many of these in this column over the years but before we review three key ones, let’s get a better understanding of what causes a fire to occur in stored grain. The science behind it has not been fully explored and documented, so there are many opinions and speculations circulating.
Self-heating, thermal decomposition of stored grain
During my trips to Africa, it is common to see people gathering wood and making charcoal that they sell in large bags along the roadside. Wood is either stacked in the shape of a beehive (or igloo) or packed in a dug-out soil pit and then covered with a layer of soil to create an airtight seal. In both so-called mound and pit kilns, room is left at opposite ends for an air inlet and outlet, and the material is ignited on one end. Once a strong fire is going, air entry is controlled to enter on one side and exit on the other, causing the combustion region to gradually move through the pile. Thus, the heat (energy) for the carbonization process is supplied by combusting part of the wood itself and controlling the amount of air into and exhaust out of the pile. The kiln has to be tended constantly over the next several days, opening and closing holes in the soil layer to control the amount of air. Once the carbonization process is complete, the mound or pit kilns are uncovered and the charcoal is allowed to cool. It occurred to me that the process of grain self-heating and potentially smoldering, and at times igniting into an actual fire and burning, is rather similar to the charcoaling process.
Charcoaling is a so-called slow pyrolysis process of heating wood or organic material (that contain cellulose, hemicellulose and lignin components, all a form of starch that is a major constituent in corn and other grains) in the absence of oxygen and over a long reaction time (days). The process has been used for thousands of years for the conversion of wood into charcoal. It generally takes place in three phases:
- Dehydration — Above 100°C (212°F), the water trapped in the pores of the biomass is evaporating and driven off as hot vapor. In the case of grains, storage moisture contents of 13% to 17% are reduced to near zero.
- Thermal decomposition — Thermal decomposition starts between 260°C and 300°C (500°F to 572°F). The cellulose, hemicellulose and lignin components of the dried-out biomass break down and carbonize. Volatile constituents are released. If disturbed during this phase and air enters, combustion may take place.
- Cooling — After thermal decomposition is complete, the charred biomass needs to cool. The cooling phase takes much longer than the thermal decomposition (i.e., carbonization) phase.
Stored grain is a porous material with an air void space (porosity) ranging from 45% to 50% in rice and barley to 40% to 45% in corn and wheat, to 35% to 40% in round kernel grains such as soybeans, sorghum and canola. The absence of oxygen results from mold spores enveloping grain kernels, filling in the airspace between kernels and caking an ever-growing grain mass together.
At the center of that grain mass is the self-heating “hot spot” that begins to brown and then blacken grain kernels as a result of mold spores feeding on the starch and oil. Oxygen is used up while grain temperature increases as does the generation of CO2 and moisture due to the respiration of the mold spores converting starch and oil into heat, water and carbon dioxide. Unless a temperature sensor is near the “hot spot,” it will take much more time for temperature cables to pick up the self-heating of the grain than CO2 sensing, which is excellent for detecting the early onset of spoilage in a stored grain mass.
It is true that stored product insects can also cause “hot spots” (especially in summer-harvested crops such as wheat). Insects that feed on mold spores (i.e., hairy fungus beetle, foreign grain beetle) will contribute to generating a mold-induced “hot spot.” Both stored product insects and mold species have optimum reproduction and development ranges and begin to die at threshold temperatures of 45°C to 50°C (113°F to122°F). As the mycelium created by the mold spores fills in the air void spaces around the infected kernels and seals in the heat, the biochemical self-heating process stops once oxygen is depleted and moisture is evaporated, and the thermochemical pyrolysis process begins to take over.
According to references describing slow pyrolysis, “wood becomes brown at 220°C (428°F), a deep brown-black after some time at 280°C (536°F), and an easily powdered mass at 310°C (590°F). Charcoal made at 300°C (572°F) is brown, soft and friable, and readily inflames at 380°C (716°F); made at higher temperatures it is hard and brittle and does not fire until heated to about 700°C (1,292°F).”
The key to successfully completing charcoaling is to maintain an airtight seal until the slow pyrolysis process has converted the woody biomass before the resulting charcoal is allowed to cool off. If the charcoaling process is disturbed before it is done (i.e., the airtight seal breaks open and oxygen enters), the charcoal will catch on fire. Thus, it would seem that as long as a self-heating grain mass that has entered the slow pyrolysis process is not disturbed, a flame will not ignite and cause a fire.
Furthermore, the volume of grain undergoing slow pyrolysis may be sufficiently insulated by surrounding grain that the process may complete all the way without causing further damage to the rest of the stored grain mass. This has been evidenced in silos where columns of blackened grain never ignited because of the presumably airtight seal of the mold mycelium, the insulating properties of the surrounding grain, and the lack of forced air flow due to aeration.
Cable sensors outside of the thermally decomposing grain will be slow to indicate the high temperatures in that volume, potentially misleading the stored grain manager into a false sense of security. The moment unloading of the grain mass is initiated and the charcoaling grain volume is disturbed, exposing it to oxygen contained in the surrounding air void space, flames ignite and start a fire, which is further inflamed if aeration fans are turned on.
Best practices
In addition to the best practices to monitor and maintain stored grain shared in previous columns, the three key practices to prevent self-heating, slow pyrolysis and fires in stored grain are:
- Maintain grain at the safe storage moisture content recommended for the prevailing climatic conditions at your geographic location. Safe storage moisture content is determined by the temperature that keeps the relative humidity of the air within the stored grain mass below 70% whether the aeration fan is on or off. Seventy percent relative humidity is the generally accepted limit that keeps molds from sporulating and causing the onset of grain spoilage. Safe storage moisture content can be conveniently determined with the help of the Grain Aeration & Storage smart phone app that we introduced in this column in the November 2020 issue.
- Mitigate insect presence by keeping grain as cool as feasible for the prevailing climatic conditions at your geographic location. If grain cannot be cooled or maintained below the minimum threshold temperature for insect reproduction and development of 15°C to 17°C (59°C to 63°F), grain should be utilized before self-heating is observed, moved (or turned) as soon as self-heating occurs, or fumigated to ideally kill all life stages of infesting insects.
- Monitor stored grain using carbon dioxide (CO2) sensors that are ideally permanently installed in the headspace (and plenum) of the storage structure or are hand-held to regularly check exhaust air streams from the storage structure. Concentrations below 600 ppm are a generally accepted limit indicating that molds are not sporulating and causing the onset of grain spoilage. Concentrations of 600 to 1,500 ppm indicate on-set of mold growth, insect presence, or moisture infiltration. Concentrations of 1,500 to 4,000 ppm and beyond clearly indicate severe mold infection and/or insect infestation.
Containment
According to the recommended initial response plan outlined in the Nationwide Mutual Insurance white paper, once it has been determined that a fire is about to start or is already in progress, it is critical to take immediate steps to prevent the fire from igniting or containing the fire from spreading.
Once on fire, stored grain burns slow but extremely hot. The following steps are the ones most recommended in the industry. These can and should be completed by grain elevator personnel immediately after notifying emergency response services.
- Turn off power to the structure.
- Attempt to cover all aeration fans or ducts to shut off supply of air to the fire.
- Do not seal the roof vents in the top of the storage structure as that will cause pressure to build.
- Avoid putting water on a grain storage structure fire.
- Be mindful of continuing issues with dust explosions as well as steam explosion when spraying water on heating, smoldering or burning grain.
- Be safe and call a salvage expert – if for no other reason than to provide additional situation analysis and advice in support of local emergency response services that often are not trained in responding to stored grain fires.
Key to preserving quality of stored grain is understanding that mold (or fungal) spores are activated more so by the relative humidity of air surrounding grain kernels than temperature. A relative humidity above 65% to 70% is the general activation threshold.
This implies that moisture contents in equilibrium with a relative humidity of 65% to 70% at any temperature determines whether fungi will grow or grain will continue to store safely.
Monitoring stored grain with sensing technologies and monitoring systems that can track temperature, moisture content, and carbon dioxide is critical to early detect and mitigate the onset of spoilage and self-heating. Most storage problems are caused by moisture infiltration and insect penetration into the storage structure, which cause biological respiration from germs, fungi, and insects to increase.
Eventually the biochemical respiration process gives way to the thermochemical pyrolysis process, and when disturbed and/or aerated, oxygen can ignite and inflame the charcoaling grain mass.
Do not underestimate the challenges and dangers associated with containing a stored grain fire.
Dirk E. Maier is a post-harvest engineer with the Iowa Grain Quality Initiative at Iowa State University. He may be reached at dmaier@iastate.edu.
Source: World Grain
AUG
2021
About the Author: